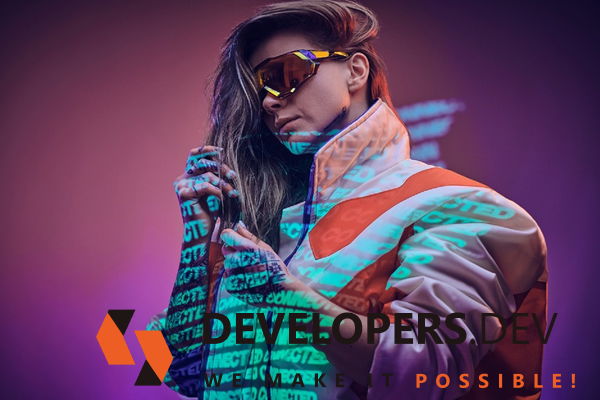
For several years now, manufacturing sector companies, particularly production managers in industrial facilities, have seen increasing interest in augmented and virtual reality technology.
Understanding its benefits and drawbacks is crucial when considering AR/VR for daily work activities; here, we present an overview of this topic. Their advantages, as well as any issues to resolve, will also be covered in detail in this blog.
Augmented Reality (AR) has revolutionized manufacturing. AR helps manufacturers reduce expenses, streamline processes, and boost production.
ABI Research estimates that by 2025 alone, industrial businesses will ship 27 million AR smart glasses.
Precision and attention to detail are integral aspects of manufacturing operations, where even minor mistakes can lead to substantial financial losses for an organization.
Smart glasses with augmented reality features can assist employees in doing tasks faster and more accurately while decreasing errors and strengthening quality control measures.
This post will describe augmented reality manufacturing and how it may be applied in manufacturing industry settings, give examples of successful applications, and highlight its many advantages.
Let's get going!
What Is AR And VR?
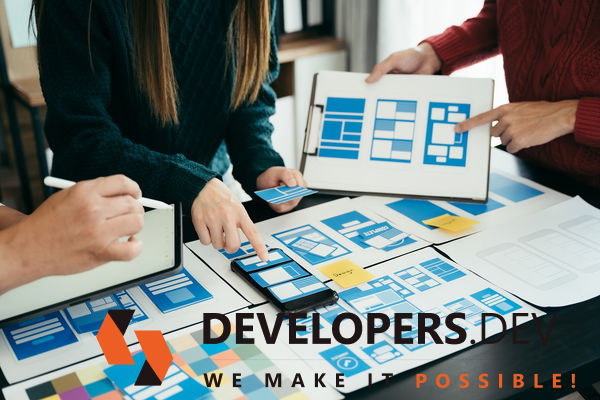
Users can have immersive experiences with AR and VR technologies. Virtual reality (VR) replicates an entirely virtual world, whereas augmented reality (AR) overlays digital information in the real world.
Both technologies generate an immersive experience using tablets, smartphones, and headphones.
AR And VR In Manufacturing
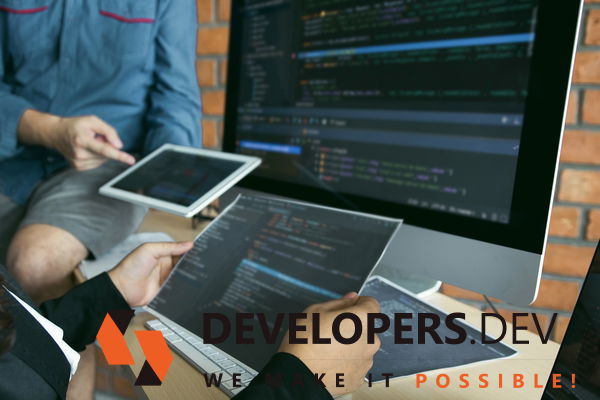
There are numerous applications for AR and VR in manufacturing.
Typical uses for them include:
-
Training: Using AR and VR, employees can be trained on intricate procedures and processes.
This enables workers to obtain experience in a secure virtual setting before carrying out the task in an actual one.
- Design: Products can be designed and prototyped using AR and VR. This allows designers to see the final product in three dimensions and make adjustments before it is produced.
- Maintenance: AR and VR can help with repairs and maintenance. By providing technicians with information and directions while they work on repairs, maintenance may be completed in less time.
- Quality Control: Products can be inspected for flaws using AR and VR. This lowers the possibility of errors in the finished product by enabling speedier and more precise checks.
Benefits Of AR And VR In Manufacturing
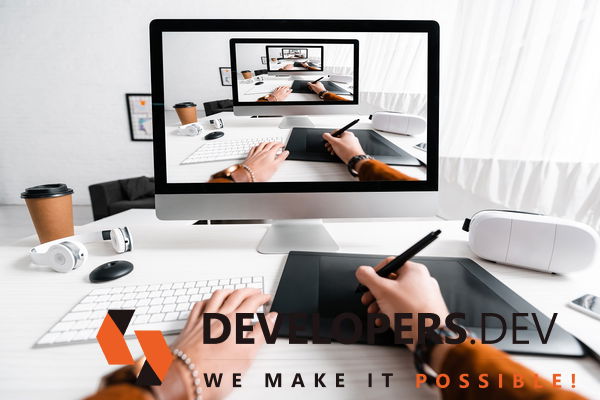
There are several advantages of AR and VR in production, such as:
- Increased Efficiency: Numerous procedures can be streamlined with AR and VR, enabling quicker and more precise operations. For example, employees can utilize augmented reality (AR) to obtain information and instructions without leaving their workstations, which cuts down on the time it takes to complete activities.
- Improved Safety: Virtual and augmented reality allow workers to receive training and practice in a safe environment, lowering the possibility of mishaps and injuries, especially for jobs that are dangerous by nature.
- Enhanced Design: Thanks to AR and VR technologies, designers may make adjustments and see a product in three dimensions before it is created. This can enhance the finished product while reducing prototype time and expense.
- Increased Quality: AR and VR can raise quality by enabling more precise inspections and reducing the possibility of flaws in the finished product.
Challenges Of AR And VR In Manufacturing

Although AR and VR have much to offer, several issues must be resolved before using these technologies in production.
Typical difficulties include the following:
- Cost: Technologies like AR and VR can be costly, mainly when you include the price of the hardware and software.
- Integration: AR and VR technologies must be integrated with current systems and procedures. This can be difficult, especially if you're working with outdated technology.
- Training: Employees need to receive training to effectively use AR and VR technology. This can be costly and time-consuming.
- Security: AR and VR systems can provide security vulnerabilities if not adequately secured. This includes risks like data breaches and illegal access to private data.
The manufacturing sector may greatly benefit from AR and VR technology, including higher productivity, safety, quality, and design.
Nonetheless, other issues need to be resolved, such as integration, security, cost, and training. It's critical for production managers in industrial manufacturing facilities to comprehend these advantages and disadvantages when deciding whether or not AR and VR technology implementation is the best course of action for their company.
Also Read: The Future Of AR/VR: Challenges & Opportunities? $Trillions Await!
Five Applications Of Augmented Reality In Manufacturing For Maintenance And Assembly
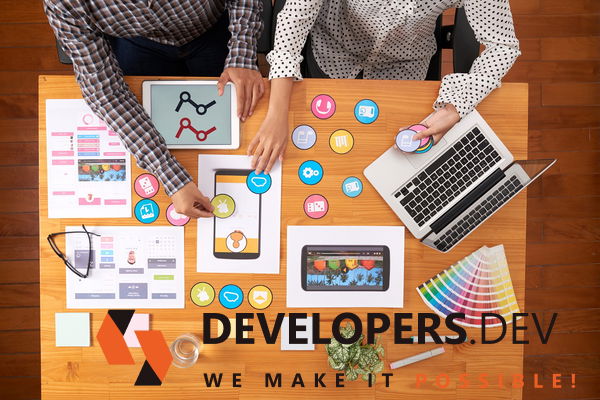
Five examples of how factories are utilizing augmented reality (AR) to improve productivity are as follows:
Training And Upskilling
Companies will need to upgrade the skills of 50% of their present workforce as they adopt new technology. However, AR can assist businesses in giving their employees an immersive learning environment.
Workers can interact with virtual objects in real-time and listen to more information about them. Additionally, all of the training materials may be created once and added to a single database.
Employees can then access them at any time and from any location.
Digital Work Instructions
Workers in manufacturing operations must complete complex tasks. Additionally, correcting employees frequently takes at least a few tries.
AR can minimize these mistakes by superimposing instructions directly onto the work surface. Employees can follow one instruction at a time and cut down on errors.
AR-based instructions, which can augment 3D projections with audio cues through an easy-to-use interface, also make documenting instructions easier.
Prototyping
Product development is a costly and time-consuming procedure. Businesses frequently invest up to USD 30,000 on a single prototype.
Before being authorized for production, this model is subject to multiple inspections and modifications.
AR makes prototyping easier, enabling designers to see their creations functioning in the actual environment. As a result, the price of physical prototyping decreases.
Quality Assurance
AR enables employees to display 3D prototype visuals on any surface, allowing them to verify quality assurance throughout production quickly.
Continuous Maintenance
Daily users of machines are more likely to require repair because of wear and tear. AR shortens the time needed for these regular maintenance by making information more easily accessible.
Which kinds of Augmented Reality Technology Are Employed In Manufacturing?
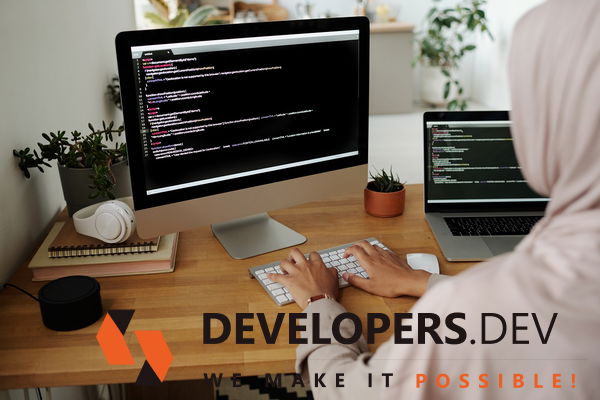
Describing the three types of augmented reality interfaces:
Tablet AR
In this case, the user interacts with digital objects using a tablet or smartphone with a specific augmented reality app.
The technology is helpful for basic augmented reality tasks like production monitoring. These tasks don't require intricate interactions with virtual items.
Furthermore, using a tablet is comfortable because there is little time spent staring at a screen.
Besides, the majority of people already know how to use a tablet. To put things in perspective, there were 1.28 billion tablet users globally in 2021.
Because of this, deploying tablets necessitates less employee training, which saves money.
Wearable AR
In this case, the user uses glasses or a headset to interact with digital things. Because the technology is worn, the operator does not need to hold a handheld device or controller.
Instead, the user can accomplish tasks in real-time and overlay digital data over real-world items using augmented reality (AR).
Equipment maintenance and other production processes make use of wearable augmented reality. As a result, more time is needed, flipping between the task at hand and consulting a manual.
It also cuts down on maintenance time. That comes to around forty hours a week for certain companies.
Projected AR
The interactive AR item can be viewed on any surface. The technology allows for simultaneous viewing by numerous users, making it useful for various tasks like maintenance, testing, training, and inspection.
This AR technology simplifies several production procedures.
Conclusion
Undoubtedly, integrating AR and VR into industrial manufacturing will take time and money. It also entails overcoming obstacles like designating regions for its deployment, incorporating it with outdated hardware, providing employee support, etc.
The best practices for implementing AR/VR at the corporate scale entail starting with a pilot project and proceeding based on its results.
In summary, incorporating Virtual Reality (VR) and Augmented Reality (AR) technology into production processes signifies a revolutionary change towards accuracy, efficiency, and creativity.
Manufacturers may reduce errors and downtime, optimize worker training, improve product design and prototyping, and streamline production processes using AR/VR technologies. These immersive experiences provided by these technologies allow for real-time data visualization, remote help, and simulation, allowing employees to make well-informed decisions and maximize workflow efficiency.
With the growing capabilities of AR and VR, manufacturing will embrace these technologies more widely, boosting productivity, quality, and the industry's overall competitiveness. By promoting continuous improvement and influencing the design of future factories, embracing AR/VR can completely transform conventional manufacturing paradigms.