
Heres where quality evaluation comes into play. Manufacturing companies can utilize business process streamlining software to perform operations more simply and effectively.
Enterprise Resource Planning (ERP) Real-time data tracking, tracing, central data storage, and integration of all business growth operations are all made possible by the software.
Different modules can be used to simplify the work of each department.
Whats the Quality Control and Assurance Module within ERP?
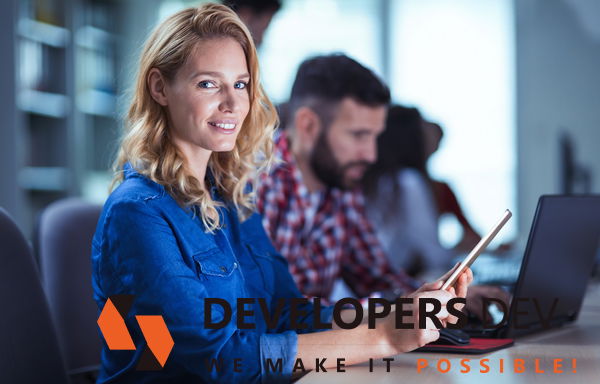
The Quality Control & Assurance module ensures that all materials, stores, production modules, and quality checks are in sync.
This module allows you to set control parameters for products or processes. This module keeps track of all material received from suppliers and shipped to customers. This module records rejection reasons and helps you evaluate a supplier or process.
The quality control module monitors the quality of work orders that are currently being placed on shop floors. ERP is used to control the quality of products. Lets look at how ERP integration can benefit quality-related functions in businesses.
Businesses looking to succeed and maintain customer loyalty in an ever-evolving market must produce products of uncompromising quality, which means monitoring product quality throughout their supply chain management - enterprise software resource planning (ERP) systems provide invaluable assistance here.
Companies using ERP software for quality control typically experience an impressive 20-25% reduction in defects on average and 25-275% increases in customer satisfaction scores - figures demonstrating just how significant ERP can be in providing consistently superior products to consumers.
ERP (Enterprise Resource Planning) systems are the central hubs that streamline business goals operations while allowing businesses to track quality easily.
ERP provides comprehensive capabilities from setting quality parameters to monitoring them and implementing controls over quality measures.
Businesses can proactively address trends and problems by creating insightful reports. In addition, analytics is also an option available to them when producing informative documents.
This article will focus on using ERP systems efficiently for product quality tracking. In particular, we will look at essential features and techniques available as part of an ERP solution while offering valuable insight to assist companies in overcoming potential hurdles.
ERP: Introduction and Role of ERP in the Management of Various Business Operations
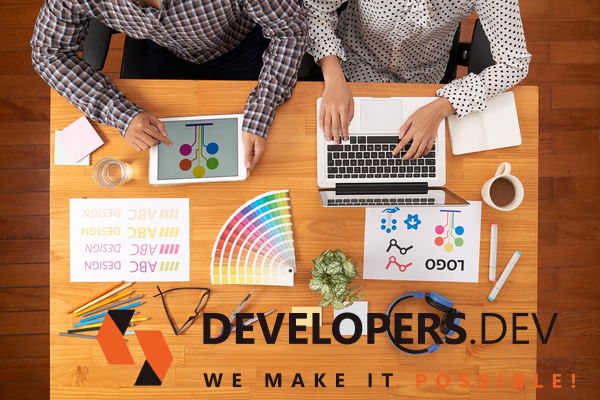
Enterprise Resource Planning (ERP) technologies have transformed how businesses operate, including product quality tracking.
ERP is a software package that integrates various aspects of operations - manufacturing, financial management, customer relationship management (CRM), inventory management control (IC), finance (Finance), and HR - all into one cohesive package.
ERP systems serve as an indispensable platform for monitoring product quality. Businesses use them to control quality management effectively while monitoring it during all production steps using modules and features explicitly tracking it.
ERP systems are central in tracking quality by setting quality parameters for every product or service the business offers.
These parameters define specifications and standards which products must meet to qualify as acceptable - an area in which businesses may customize or configure these parameters according to customer needs and industry norms.
After defining quality parameters, an ERP system can aid businesses in implementing quality control procedures. Companies using such an application can track product-related information such as test results, inspection reports, and incidents of non-conformance directly into an ERP system for real-time insight into metrics related to quality metrics.
Integrating quality tracking modules into their ERP allows businesses to generate detailed reports, analytics and reports about product quality issues and trends and highlight areas for improvement.
With access to this data, companies can make informed decisions and take proactive measures toward increasing product quality.
ERP systems can integrate easily with quality assurance tools like Statistical Process Control Software (SPC) or Quality Management Systems (QMS), further strengthening their capabilities for businesses to take advantage of advanced statistical analyses, comprehensive examination, corrective actions, and preventive preventative steps.
ERP systems are essential in streamlining various business processes, including quality tracking. ERPs serve as a central platform that establishes quality parameters, implements quality control procedures, and captures real-time data collection - producing insightful reports and being fully compatible with tools explicitly designed to ensure quality.
ERP quality tracking enables businesses to increase customer satisfaction by maintaining consistent quality levels across their accounting operations.
Want More Information About Our Services? Talk to Our Consultants!
ERP and Quality Control
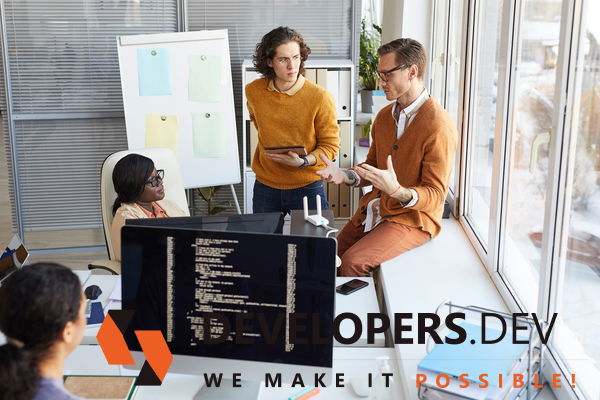
Regarding quality control, Enterprise Resource Planning software systems play a vital role by streamlining processes efficiently and unifying various functions into an effective quality monitoring strategy.
Businesses using an ERP can implement adequate quality controls across their production cycle while monitoring product quality during every production stage. This section will examine how an ERP system can assist businesses in providing consistently superior products.
ERP Systems Can Simplify Quality Control
ERP systems offer powerful functionalities and tools that help streamline quality control procedures and facilitate accurate tracking of products.
Here are a few ways ERPs can reduce quality control processes:
-
Centralized Data Management- ERP systems centralize information across departments and processes into one quality data repository.
They eliminate the need for multiple standalone systems or spreadsheets while offering seamless access to quality information in real-time.
- Standardized Parameters- ERP Systems allow companies to define standardized quality parameters for products and processes using specifications, tolerances, and criteria that define acceptable levels of quality. Centralizing and standardizing parameters through ERP can aid companies with quality control by maintaining consistency over time.
- Automation of Quality Inspection- ERP systems enables automation to reduce manual effort and errors while providing inspectors with checklists, criteria, and workflows to guide them and adhere to quality standards.
- Quality monitoring- in ERP systems provides real-time information about quality at each step in production, so businesses can effectively track it, detect deviations quickly, and correct them immediately, thus preventing quality issues from worsening.
- ERP systems offer practical tools for non-conformance management- When an incident of non-conformance arises, workflows will automatically initiate in response. Investigate, document, and resolve incidents as soon as they appear, ensuring timely corrective action, preventive measure implementations, or root cause analysis analyses are completed as quickly as possible.
- Supplier Quality Control- ERP systems allow firms to track and assess the performance of its suppliers. This includes managing non-conformances and audits as well as overseeing certifications.
- Document Control and Compliance- ERP systems offer document control support by managing documents related to quality, such as standard operating procedures, work instructions, and quality manuals. Employees can quickly access approved and up-to-date records while compliance is ensured with standards and regulations.
- Analytics and Reporting- ERP systems feature sophisticated analytical capabilities that enable businesses to produce comprehensive quality reports that reveal insights on quality trends, metrics, and improvement areas - providing data-driven decisions and continual quality enhancement.
ERP systems can streamline the quality control process by taking advantage of their features and functionalities, enabling companies to track and manage quality better.
As a result, businesses experience higher customer satisfaction ratings, operational efficiency improvements, and enhanced market competitiveness.
ERP Systems That Are Easy To Track And Use Feature Numerous Features
They are designed to facilitate tracking and controlling quality at every stage in production processes. Key modules enable companies to monitor product quality throughout each step in the manufacturing process.
Here are the essential modules and features of an ERP that allows quality tracking:
Quality Control Module: Designed exclusively to manage quality, the Quality Control module of an ERP system serves as the hub of all quality-related activity within an enterprise.
Companies use it to set quality parameters, perform inspections, track metrics, handle non-conformances effectively and manage non-conformances efficiently. This hub serves as the center for quality-related activity within its system.
Document Control Module: This module organizes and controls versions of documents related to quality, such as Standard Operating Procedures (SOP), Work Instructions, and Quality Manuals, to maintain current, approved copies that meet quality standards.
Businesses using this system ensure their documents meet current compliance standards while remaining compliant.
Module for Supplier Management: Businesses The Module for Supplier Management provides businesses with an effective means to evaluate and track supplier performance.
Companies using it can determine the quality performance of suppliers, manage certifications for them, perform audits on materials they supply, or record incidents of non-conformance, all to ensure suppliers meet quality standards while contributing towards more excellent overall product quality.
Module for Inspection and Testing: This module makes creating inspection checklists and criteria simple by offering workflows and other functions, recording results of inspections performed, tests run, and measurements taken.
Businesses using this system can record inspection results easily while performing tests and taking measures without manual effort - creating consistent quality standards while streamlining inspection processes.
Module for NNon-Conformance This module was created to assist businesses with managing and tracking quality issues in a business intelligence setting.
By creating workflows for investigation, documentation of causes, corrective action, and preventive measures monitoring; as well as monitoring preventive measures - this module supports efforts toward increasing quality while efficiently handling deviations and deviations.
Module for Analytics and Reporting: This module offers robust analytical and reporting capabilities to monitor quality.
Businesses can use it to produce quality reports, identify trends and areas for improvement, and gain insight into metrics like defect rates, customer complaints, and variations in processes - providing data-driven decision-making capabilities for better decision-making processes.
Recall and Traceability Management: ERP systems typically include recall and traceability management features that allow businesses to track raw materials, finished products, and components throughout their supply chains to identify any quality problems or recalls that arise and take immediate steps to mitigate risks.
Midsize Businesses can easily trace product origins if issues occur and take necessary measures to minimize them.
An ERP system provides an ideal tool to monitor, assess and track product quality. The tracking rate can become simpler by centralizing and integrating this capability within an ERP system.
At the same time, visibility increases while continuous improvements occur over time.
Read More: All about ERP Software for Accounting & Finance Productivity
Establish Quality Parameters in an ERP System
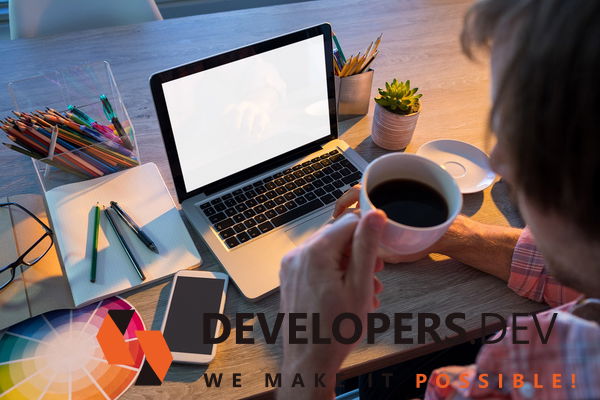
Setting quality parameters accurately reflecting product and process quality tracking requires precise, standardized parameters.
ERP systems play a pivotal role here by offering companies tools and functionalities needed to configure and define quality parameters explicitly tailored for individual products or processes.
This section discusses the need to set quality parameters within an ERP system and the steps needed for maintaining uniform and consistent product quality control.
Establishing the Quality of Your Product
To properly establish quality parameters in an ERP, several steps must be completed to align them with customer standards, needs, and internal quality goals.
Understanding Product Requirements: Start by understanding your product requirements for maximum success, considering factors like functionality, durability, and aesthetics when creating this list of specifications.
Establish Key Quality Characteristics Determine Critical Quality Features (CCFs): We must identify those key quality features of our product or service that have an immediate effect on customer satisfaction and performance, attributes or characteristics that must be closely monitored to maintain a consistent level of quality over time.
Determine Quality Metrics: Establish metrics for measuring and assessing identified quality characteristics.
Metrics could range from quantitative measures like dimensions and weights to performance indicators or qualitative assessments using sensory evaluation, visual inspection, or other means.
Establish Acceptance Criteria: To establish acceptable ranges and thresholds for quality measures, its necessary to establish acceptance criteria.
Acceptable wide ranges or points indicate whether a product can be considered satisfactory by industry standards, client specifications, or internal quality goals.
Set Quality Parameters in ERP: Use the ERP quality management module to configure quality metrics, acceptability criteria, and any additional rules needed for tracking product quality.
Validate and Test Quality Parameters: Test and validate quality parameters to reflect product quality accurately.
To achieve this verification process, it may be necessary to conduct pilot tests or sample testing against benchmarks or reference samples.
Document Parameters: Create a record that details all parameters and standards associated with quality for every product you manufacture; that can serve as an invaluable guide for quality control staff and can easily be updated as required.
This documentation performs both functions at once.
Train and Communicate: Once quality parameters have been defined, they should be communicated to all relevant parties, such as production staff, quality control personnel, and (where relevant) suppliers.
Provide training on monitoring best and applying these parameters within your ERP system.
Businesses can benefit from following these steps to establish comprehensive and accurate quality parameters for their product, with the ERP system helping companies to streamline this process to ensure standardization and consistency, providing easy access to quality parameters crucial in tracking quality throughout the production cycle.
Configuring ERP to Include Quality Parameters
To achieve seamless integration, specific steps must be taken when setting up the ERP system to include quality parameters in management processes.
This guide demonstrates how this can be accomplished.
Navigating to Quality Management Module: Navigate directly into the quality management module within an ERP system specifically created to handle quality control and configuration processes.
Define Metrics: Within this module, you can identify quality metrics aligned with your products critical characteristics - dimensions, specifications, indicators of performance, or any other quantifiable attributes may all be included as relevant quality measurements.
Set Acceptance Criteria: Each quality measure must establish clear acceptance criteria. Incorporate these into an ERP system.
Create Inspection Checklists: Establish inspection checklists based on quality metrics and acceptance criteria to guide inspection processes and ensure all critical quality parameters are tested during checks.
This way, inspectors can ensure all relevant parameters are thoroughly evaluated during an examination process.
Workflow Creation: Develop workflows within an ERP to manage information related to quality and processes, such as initiating inspections, performing root cause analyses, implementing corrective actions quickly, and checking on their effectiveness.
Integrate With Measuring and Testing Equipment: When applicable, integrate an ERP development System with measuring and testing equipment for direct data entry and automatic measurement result transfer directly into it, reducing human resource management functions errors and increasing efficiency.
Utilize Traceability Features: Take advantage of the ERP systems traceability functions for tracking materials and components during each production stage to guarantee quality across the board.
The rate must be kept a priority throughout.
Customize Analytics: Create comprehensive reports, dashboards, and insights on quality metrics and trends, providing data-driven decisions and initiatives for continuous improvement.
Establish user roles and train users: All users interacting with the ERP quality management module should receive appropriate training on its configurations, data input processes, inspection processes, reporting formats, and reporting forms.
In addition, set user permissions/roles accordingly to guarantee correct data access.
Review Parameters Regularly: It is wise to regularly evaluate and update the parameters within an ERP system in light of changing industry standards, customer demands, or internal quality goals.
Document any revisions by maintaining version control documentation.
Following these steps will enable business leaders to configure their ERP systems in such a way as to incorporate quality parameters and simplify quality control, serving as a central platform to monitor product quality while supporting consistent standardization and continuous improvement efforts.
Implementing Quality Control Processes
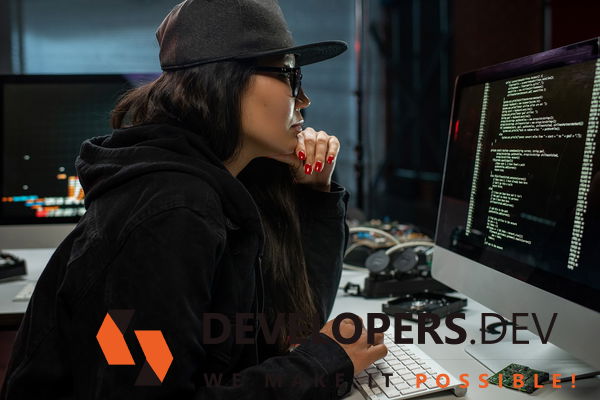
Once an organization has decided on adequate quality controls, its next step should be defining and configuring quality parameters within an ERP.
In this section, we explore how quality controls are implemented within an organization using the capabilities of an ERP. We will examine the steps of quality control to achieve consistent product quality.
Implementing Quality Assurance Processes in ERP Systems
Implementing quality assurance processes within an ERP system involves several steps for effective product quality monitoring and management, including implementing quality control.
Here are the main ones:
Define and Plan Quality Control Procedures: To begin the quality control procedures process, it is vitally important that a plan be drawn up that details their use - this should include frequency of inspections, methods used, and goals and roles of personnel involved.
Configure Checklists Utilize The ERP inspection module generates checklists tailored specifically to quality parameters, covering essential quality attributes.
Your lists must guide inspectors throughout their inspection processes.
Quality Inspections Utilizing: an ERP system to carry out regular quality control inspections will enable you to achieve defined quality parameters.
Inspectors can enter inspection results and measurements into this platform and document deviations or errors from established quality parameters.
Capture Real-time Data: Use an ERP system to capture quality data in real time throughout the entire production process, such as inspection results, measurements, test reports, and any information related to quality.
Make sure data can be entered quickly and accurately for tracking and analysis.
Track NNon-conformanceUtilise: The ERPs non-conformance tracking module to effectively and efficiently manage non-conformance.
Once deviations from quality parameters have been identified, initiate workflows in your ERP system that investigate root causes before documenting corrective action plans - follow up on their implementation to monitor their success.
Analyzing Performance and Quality Trends:
- Utilize ERPs reporting and analytics features to analyze performance and quality metrics.
- Create reports providing insight into metrics, issues that recur, areas for improvement that need further attention, etc.
- Use this data to improve product quality while driving continuous improvement initiatives.
Correct and Preventive Measures: Based on an analysis of quality data, identify trends and take corrective or preventive actions as needed based on ERP tracking tools for tracking these measures and managing these actions - this will enable timely resolution or prevention of quality issues.
Monitor and Improve:
- Evaluate and assess the quality of processes implemented within an cloud-based ERP system.
- Seek input from key stakeholders.
- Conduct internal audits using data-driven insights to pinpoint areas requiring further optimization or enhancement, as well as conduct regular internal audits to monitor processes implemented therein.
Inspection, data collection, non-conformance monitoring, and analytics capabilities provided by this system enable practical analysis and tracking of product quality resulting in enhanced customer satisfaction, operational costs efficiencies, and market competitiveness.
How Can Businesses Leverage ERP For Quality Control And Assurance?
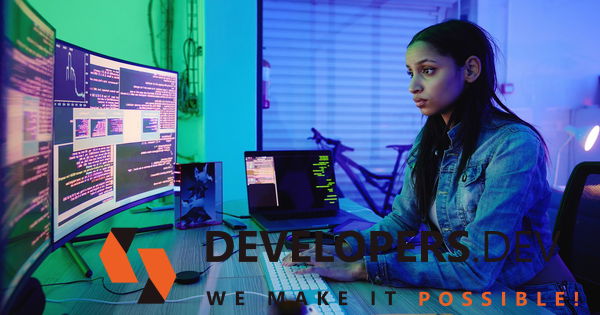
#1. Keep Your Documentation Current
To ensure product specifications are consistent, the business performance defines quality metrics. The platform allows process owners to automate tasks such as auditing incoming materials to verify that your business units quality standards are met.
ERP software solutions can track the quality of raw materials and finished goods for products coming in and going out. This module ensures that all supply chain functions are performed with the same performance indicators and metrics.
Maintaining standards across products and processes with real-time tracking via a central database is easier.
#2. Increases Customer Satisfaction
Customers expect high-quality services and products from the service providers they choose. To ensure they meet the quality standards, businesses use the Quality Control and Assurance module at all stages of production.
This database provides insight that helps to identify improvement areas and direct efforts in the right direction. ERP scalable solutions allow businesses to manage quality from raw material procurement through production and distribution.
An ERP will ensure that the production facility only sends out acceptable products, guaranteeing 100% customer satisfaction.
#3. Define Testing Criteria
ERP quality control allows you to define testing parameters based on customer/business size needs. The ERP Quality Control module can then be configured to automate test mapping, tolerance percentages, test parameters, and generating test results.
Products that fail to pass the test are added to the reject list and processed according to the SOPs.
#4. Product Quality Inspection
Manufacturers perform quality testing on every product that goes through their production lines. Integration of ERP allows users to generate test reports and link test results with production or purchase orders.
Due dates can also be set for all tests. ERP integration allows everyone within the company to access test results based on their access rights.
#5. Supplier Relationships
It is essential to ensure high quality by closely monitoring the suppliers compliance with the standards. This is especially challenging for companies that must keep an eye on suppliers.
Integrating a discrete manufacturing ERP system provides updates on quality metrics, inbound shipment inspections, and other relevant information. Managers are kept informed by notifications about any delays or other issues. ERP keeps track of supplier lead time and delivery to give an overview of their performance history.
ERP software helps managers choose reliable suppliers and maintain quality and compliance within the supply chain.
#6. Compliance
Conforming to regulations and standards is a crucial part of manufacturing. Manufacturers can build a solid foundation for compliance with an ERP strong solution quality control and assurance modules.
It assists businesses in meeting the requirements for packaging, manufacturing, and handling products. Manufacturers of quality assurance modules can achieve high productivity without compromising standards.
The Quality Control & Assurance module allows you to inspect material received from vendors and verify it against the labor production and delivery challans, finished goods, and other items.
The discrete manufacturing ERP software allows manufacturers to control and monitor their core business processes. Our ERP software is easy to integrate, and our training experts and customer service make us one the most trusted ERP providers for MSMEs and SMEs in India.
ERP can be used to streamline business process modeling and maintain high-quality production.
Want More Information About Our Services? Talk to Our Consultants!
Conclusion of Article
Implementing an ERP for product quality tracking can transform how businesses monitor and manage quality processes, providing companies with more accurate product data as they streamline quality control procedures and increase data accuracy.
With an ERP to track product quality processes, businesses can enhance quality by streamlining quality control procedures while improving data accuracy resulting in enhanced product quality for customers.
This article explored various uses for ERP services to monitor quality, from its role in business objective management, through configuring it and implementing quality assurance processes, all the way up to producing insightful reports and analyses.
At ERP Systems International, we understand the challenges companies can encounter when implementing an ERP system to track quality.
From integration issues and customization demands to user adoption needs and challenges, each implementation process needs careful and deliberate management for its successful outcome.