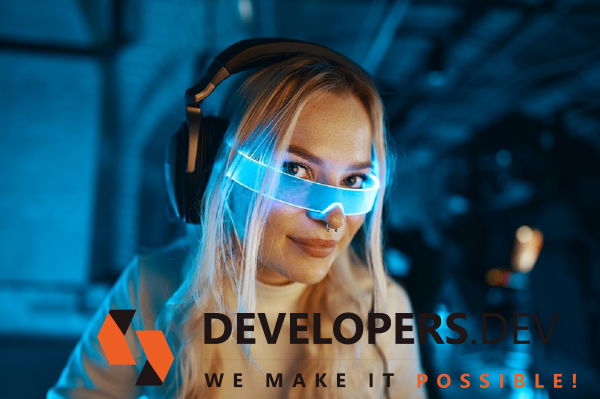
Separate groups responsible for product design and manufacturing led to unexpected engineering modifications at the end of development, impacting cost, quality, and time to market.
Designers used CAD applications, while manufacturing used CAM software for toolpath creation; as a result, data needed translation or import before production could begin; for any changes required for manufacturing, the entire process must repeat itself.
CAMWorks integrated CAD/CAM solution enables total control over manufacturing processes while offering easy design changes with automatic adaptation of toolpaths for easy changes to toolpaths, creating cost-effective manufacturing processes that improve competitiveness and productivity.
What Is CAD/CAM Software?
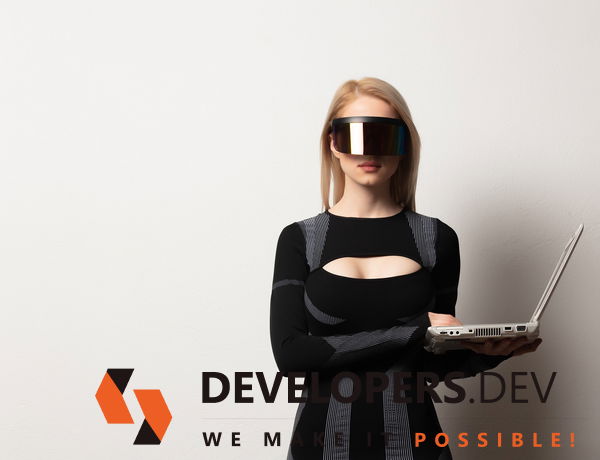
A CAD/CAM system is the result of decades of work on manufacturing process automation. It represents the goal of inventors, innovators, mathematicians, and machinists who all wish to advance the manufacturing industry with technology.
CNC Machines utilize this term when used for both design and manufacturing - Computer-Aided Design is its acronym, and Computer-Aided Manufacturing uses geometric shapes in its digital models as building material, whereas not every manufactured item requires three-dimensional solid models to construct its products either
CAD:
In CAD software, Wireframe geometries such as lines, circles, and points can be used to draw 2D parts.
In contrast, 3D surface design software enables the creation of three-dimensional surfaces to define contours that can later be transferred into CNC and CAM machines for processing. Modern CAD design software also creates parts suitable for two-, three-, four---, or five-axis CNC machining processes - thus making CAD design software essential to production as the designed components are transferred to programming software for machine programming purposes.
CAM:
Industry professionals often refer to Computer Aided Manufacturing, or Machining, as "CAM". Once a CAD model has been designed, CAM software must convert this design into machine language that can be used on milling or lathe machines (commonly referred to as G-Code).
After programming this part into machine language (G-Code), CNC Milling machines or CNC Routers use this CAM program in tandem with cutting paths calculation software that then removes excess material with cutting paths used by tooling, typically used alongside part programming for CNC Water Jets or Burning machines as well.
A computer-aided manufacturing (CAM) program must be capable of determining cutting speeds and feed rates for tools in its library, managing materials, and creating optimal toolpaths that optimize the machining of CAD models.
"Toolpaths" made through this CAD-CAM software come in all sorts of styles to be employed for drilling holes or pocketing or engraving designs - from Hole Drilling Toolpaths through 2D or 3D versions used in profiling applications or pocketing for pocketing purposes to profiling faceting pocketing or engraving applications.
CNC machines come in all varieties. Haas is one of the more well-known manufacturers. At the same time, other key players such as Hurco, Fadal, and Bridgeport also produce CNC machines.
Manual machines can easily be converted to CNC ones by adding motors, controllers, and essential components; then using CAM Software which converts all this information - such as toolpath data from manual machines into NC Code language that the CNC understands through post processors that an operator or technician can customize through CAD/CAM programming; this post-processing component plays a central role in programming CNC programming.
Origin Of CAD/CAM Software
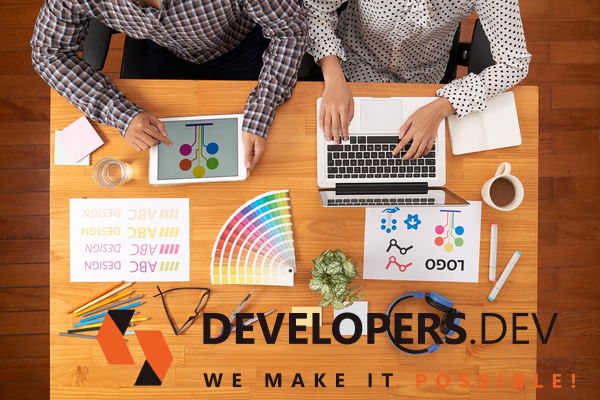
CAD/CAMs three primary operations stem from its historical roots. First was automating drawing processes at General Motors Research Laboratories during the 1960s; computer modeling is timesaving since changes can easily be made in model parameters for correction or manipulation purposes.
Simulation was another method used by high-tech industries such as semiconductors and aeronautics to implement CAD/CAM productions, leading to its prominence during the 1960s.
Numeric control proved key in improving design/manufacturing workflow during this era. Eventually, it provided numerical control as the sole link between CAD/CAM productions and design/manufacturing operations - an increasing trend today.
Read More: Software for CAD/CAM increases efficiency and expands capabilities
What Have Been The Results Of Using CAD/CAM Technology?
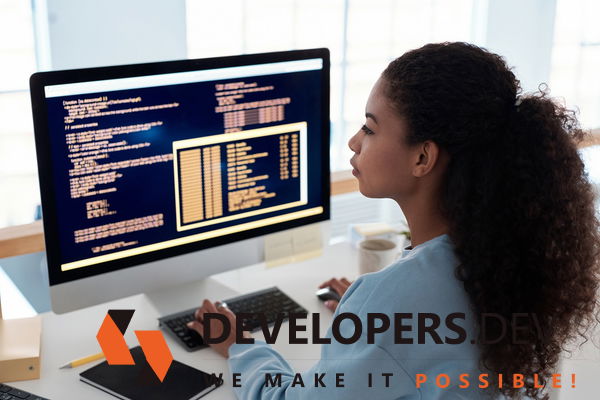
CAD/CAM was invented to answer NCs shortcomings due to its ease of use and speed; geometric data encoding systems allowed designers more effective control of production while providing seamless 3D design and manufacturing processes by eliminating production process delays significantly and expanding automated machinery usage more efficiently.
Furthermore, designers gained greater control of production. CAD/CAM integrated design and manufacturing processes into its processes for greater design control over time and reduced development times considerably.
Mass production of microprocessors and silicon chips facilitated more affordable computers. As computer prices decreased and processing power increased, CAD/CAMs use grew as prices fell as well.
While initially implemented only for large-scale production purposes, today, it can also be applied by smaller firms for production at smaller scale. Furthermore, its range has expanded considerably, with applications across numerous sectors like electronics, molded parts, and electrical components.
Software Applications Available In CAD/CAM
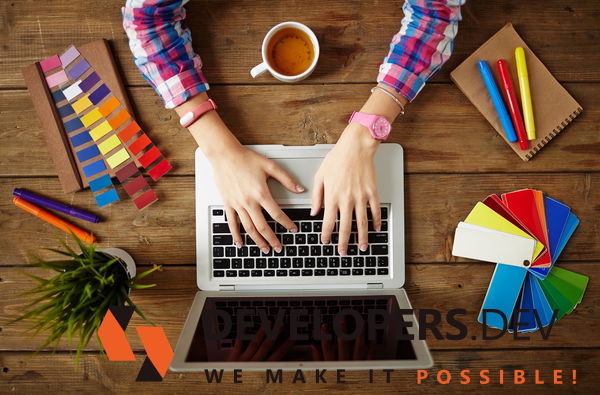
CAD allows users to simulate parts in three dimensions through production, providing a 3D simulation of their production process.
With this application, you can control angles, feed rate, clamp position, speed, machine limits, and ranges. CAD/CAMs seamless expansion has led to its widespread acceptance across industries and production processes - serving designers, manufacturers, and other production processes with valuable communication channels for efficient collaboration between design processes.
Benefits Of Utilizing CAD/CAM Software
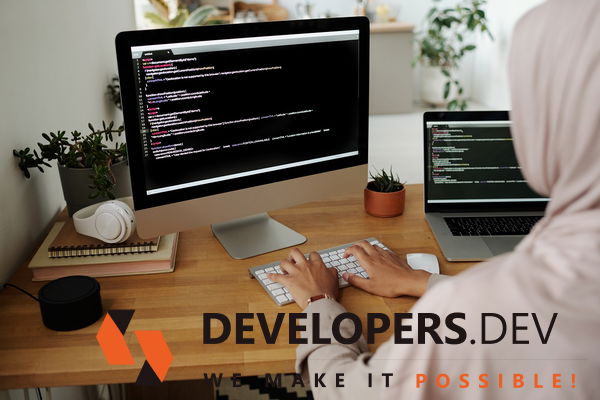
CAD modeling offers numerous advantages over traditional drawing methods using rulers, squares, and compasses. You can, for instance, easily alter a product design using CAD/CAM by erasing and redrawing its lines; zooming is also available so that magnified details may allow more thorough examination - not to mention other advantages.
There are other significant benefits as well that come from employing this form of modeling technology.
Convenience
Utilizing CAD/CAM is easy because you can rotate objects freely. By understanding all angles, CAD/CAM gives a complete sense of an objects appearance before creating and designing it to meet all requirements.
Plus, its software enables clients to preview styles earlier than traditional designs.
Rapid prototyping
Rapid prototyping allows designers to fabricate prototypes for style tests that evaluate different aspects of an item before being made entirely in metal or polymer.
This gives greater freedom when prototyping products with variable designs or pressure requirements. Rapid prototyping provides designers with real-life prototypes in minutes for style evaluation purposes - giving more freedom in prototyping processes.
Flexible application
CAD/CAM software provides rapid style changes. Before using CAM software, designers were forced to erase and redesign designs anew whenever their needs changed.
Still, with CAD/CAM, they can alter plans without needing to redraw everything again - using it even to mimic actions, for instance, simulating airflow around an engine before designing one.
Disadvantages Of CAD/CAM

Two significant drawbacks associated with CAD/CAM technology are:
High Handling Costs And Energy
CAD/CAM software consumes significant processing power on PCs. Quality components of its software can be pricey.
At the same time, smaller firms may be unable to afford its high-tech production elements. Setting up and using CAD/CAM modeling techniques also pose serious difficulties.
Complexity
Over time, CAD became more flexible. Unfortunately, with greater versatility comes greater complexity for new users to understand and utilize effectively; businesses may find CAD/CAM less appealing due to its complexity and cost implications.
Selecting CAD/CAM Software
Downloads and demos can be an ideal way to evaluate software programs, but sometimes, buying expensive yet effective versions may be best.
Before selecting the perfect piece of CAD/CAM software, extensive research must be performed - even for free programs; otherwise, you risk not finding what you need and investing in new applications sooner. Keep this list of factors in mind when making your selection:
- Your strategy will dictate whether you opt for complete CAD/CAM solutions or packages with both components included.
- Seller: Your options for purchasing your CAM device depend on whether it comes from either retailers or manufacturers; convenience can vary between these sources, too. If a local dealer offers better comfort than purchasing directly from manufacturers.
- Practice different forms of drilling; for instance, CAM drilling differs significantly from two-axis milling or three-axis contouring.
- Milling data types: 2D and 3D require specific CAM programs for processing.
Consider These Five Advantages Of Integrated Systems:
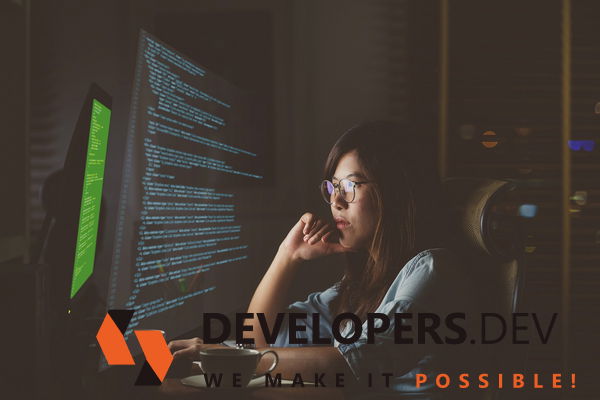
Correct Any CAD Errors Or Incorrect Data Translation
Integrating CAD/CAM eliminates costly, error-prone data translation between separate CAM applications and CAD systems, eliminating expensive translation costs and latencies or versioning problems that lead to errors.
Associative machining provides automatic updates whenever design modifications occur, saving time and resources. Integrated systems also feature associative machining, automatically updating CAM data whenever design changes occur - saving valuable rework hours.
Stay Organized When Organizing Files
Maintaining and updating separate CAD/CAM files can be challenging. In contrast, integrated software programs help organize all the information for team collaboration, faster design response, and simultaneous teamwork.
File management repositories ensure everyone uses the most up-to-date design. At the same time, an associative master model permits faster simulations, analyses, and updates to cutter paths without version conflicts.
Straightforward Process
Most standalone CAMs operate by process rather than features; after selecting the software tool and creating an operation - such as rough milling of a pocket - speed, feed rate, and other parameters like depth are entered to start making the process.
The next step in process creation would involve selecting another machine tool (perhaps to finish milling it) before repeating these steps to generate another method - then post-processing and simulating to generate G codes required for manufacturing purposes.
Programmers working with standalone CAM approach each new part individually, even if its features resemble previously programmed ones.
This often leads to five programmers having unique methods when programming one part. Standalone CAM systems promote this practice, which can result in five opinions being brought forward regarding how best to approach its programming.
An integrated CAD/CAM system helps streamline data translation.
Utilizing one interface for design and manufacturing allows for an easier design-to-manufacturing workflow while decreasing training time and IT resource requirements for managing multiple software packages.
Automate Manufacturing Processes
Automation with standalone CAM solutions such as SOLIDWORKS is impossible due to not being integrated. HCL CAMWorks integrated CAD/CAM provides automated processes using tolerances, product manufacturing data (PMI), and surface finish on 3D models as a basis to automatically generate CNC programs containing tools with appropriate speeds, feed rates, etc.
to produce optimized toolpaths (toolpaths).
Integral Software Validation Tools
Most integrated CAD/CAM software systems feature modules enabling users to validate their designs before beginning CNC machining.
G-code simulation directly within CNC programming environments is another convenient method that eliminates dry runs and drastically cuts setup times; once G-code simulation has taken place, the machine is now prepared and can begin processing, helping prevent costly collisions, programming errors, and scrap waste reduction.
Integral CAD/CAM facilitates collaboration among design and manufacturing teams through early manufacturability considerations to guarantee high-quality production, reduce errors, and cut rework costs.
Furthermore, such systems make collaboration between designers and programmers much simpler.
CAMWorks was the first fully integrated CAM software with SOLIDWORKS. As the leader of Automatic and Interactive Feature Recognition, CAMWorks provided accurate associative machining - adapting automatically to changes within models.
CAMWorks seamless integration with SOLIDWORKS makes possible:
- Consolidate and utilize one file for both CAD/CAM systems.
- Use SOLIDWORKS and CAMWorks together to generate toolpaths and the appropriate machining commands in CAMWorks.
- Solidworks geometry can generate toolpaths that ensure that the machined part is identical to what was modeled.
- Standard file formats like IGES and STP alleviate time-consuming file transfers between machines.
Top Five CAD Trends Of 2023
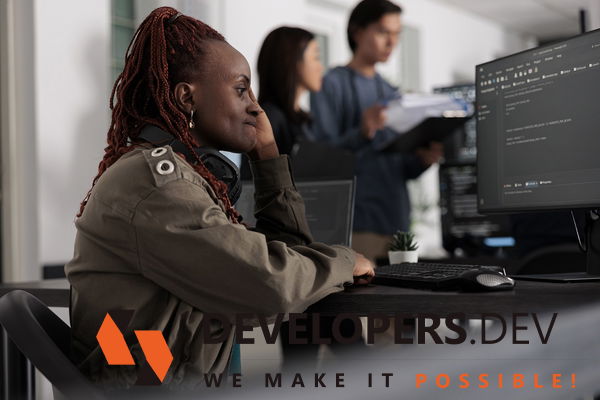
Small and mid-sized companies react differently when encountering the /CAD market, driven by manufacturers needs in response to macroeconomic developments.
Two economic trends creating uncertainty for 2023 include high global inflation rates and an undervalued Euro, making waves of unpredictability across markets worldwide.
Medium and large-sized businesses tend to be better prepared for managing this risk: they know they must continue investing through recessionary times to benefit from its inevitable recovery; small firms might spend less this coming year as an indirect response against potential stormy times ahead.
2023 will see five major trends emerge in product development. Continue reading to gain more insight.
Want More Information About Our Services? Talk to Our Consultants!
Adopting Simulation Driven Design
Simulated Driven Design should experience steady expansion throughout 2023. We anticipate designers and engineers taking more significant advantage of simulation during all design aspects to help make better-informed design decisions earlier in the process, leading to higher-quality products at reduced costs.
Digital testing enables increased innovation as companies can test a more comprehensive array of designs with digital testing technology.
Its combination with more advanced, innovative, and cost-efficient methods and user-friendly technology, such as simulation in real-time, drives SDD adoption.
SDD implementation has traditionally been hindered by disconnected tools and processes that disrupted its success.
By embedding simulation technology within CAD software solutions already used by engineers and designers, adoption becomes much more straightforward, creating one source of truth across the value chain while decreasing cycle times significantly.
Companies now have access to fast, effective design validation processes that enable rapid progress, higher quality outputs, and an expedited time to market with greater confidence.
Simulator technology gives companies more options when exploring designs versus investing in costly prototypes - increasing the probability that customers deliver optimized products more often.
Emerging Technologies, Innovation, And New Tech Solutions
Innovation in product development is driven by emerging technologies like additive manufacturing and generative designs, which substantially meet specific design goals and expand the possible definition.
Smaller companies experiment more freely with these technologies than their larger counterparts.
Generative design algorithms do not rely on human bias to provide solutions; their engine can generate solutions that often surpass what a person could come up with alone.
Generative design processes have the power to accomplish in hours what would typically require weeks for designers.
Engineers can utilize generativity generated designs in their current designs by integrating this technology with CAD tools, creating an agile process that uses all of the parametric designs advantages - an essential element to making parametric designs an engine of innovation rather than simply point solutions.
This makes generative designs an asset, not an afterthought solution.
Additive manufacturing (AM) allows companies to develop unique, impossible designs through other fabrication techniques.
Due to this potential, more companies have experimented with AM over the last decade by including design tools adapted explicitly for AM in their design processes.
Users must be empowered with technologies that seamlessly fit into existing workflows to innovate effectively and effortlessly.
Designers look for consistent levels of accuracy and sophistication across their designs regardless of geometry source or fabrication method, taking full advantage of technology best suited for the task and applying it across their plans - but without compromising how their components interact.
Drive The Digital Thread Throughout The Design Process
Companies today recognize Model-Based Enterprise (MBE). Therefore, many have implemented MBE throughout their organization by increasing CAD model use throughout all functions to increase efficiency while decreasing errors.
Most companies still rely on multiple disconnected tools in their design processes, creating inefficiencies by fragmenting digital toolchains and diminishing agility, flexibility, and efficiency.
Companies face constant pressure to bring innovative products faster to market at reduced costs as supply issues persist and competition escalates; benefits associated with embedding a digital thread throughout product development have become apparent.
This trend involves providing manufacturing deliverables directly from CAD tools, eliminating point solutions such as for machining toolpaths.
By taking this route, businesses eliminate friction points while keeping associative links alive while eliminating redundant data transference processes and save both time and effort in preparation for shop floor machining processes while decreasing errors.
Cloud Computing And SaaS
By 2023, 50 percent of enterprise applications may transition towards subscription-based offerings; 3D Modeling software vendors should continue investing in SaaS functionality and the cloud as organizations take up this trend further.
Licensing models and deployment methods of design software could see significant shifts.
The collaboration will see significant advances, too: multiple users can work simultaneously on one design in a cloud environment; it will become much more straightforward to expand to vendors, partners, and others from outside our company, making IP control much more straightforward.
Cloud computing can also increase the effectiveness of technologies like generative design. Businesses have begun using this technique to explore hundreds of possible solutions while researching only one quickly.
When customers migrate to SaaS, they automatically gain access to all new capabilities without ever needing to plan an upgrade.
Invest In Training
Training has long been an investment trend. With more businesses moving toward digitalization across their entire value chains, training industries are witnessing a revival.
Companies must upgrade their parametric modeling abilities to produce high-quality 3D models suitable for mass manufacture.
Design reuse and collaboration become more efficient by developing best practices across teams. Designers reusing designs save energy and time; however, if any models used during creation were flawed or unclear to subsequent designers, their reuse may not provide as much benefit.
However, another challenge prompting companies to invest more in training is a projected engineer shortage by 2030.
Companies of all sizes have noticed this deficit already and understand that designers must work more efficiently as competition for engineers intensifies. Retention issues arise because designers will change jobs to access training or certification opportunities; some employers require this credentialization to demonstrate reliability.
Want More Information About Our Services? Talk to Our Consultants!
Conclusion
Integration of CAD-CAM with CNC machining offers many benefits; however, you should always remain mindful of any costs incurred through implementation, processing limitations, complexity issues related to software applications being added, or other possible glitches that might arise while creating new applications.
CAD/CAM software can significantly increase design and production capabilities on many levels, from improving manufacturing capabilities to simplifying procedures - this will prove immensely helpful for your company.
Subsequent installments will cover CAD-CAM packages and how they can help transform a CAD design into CNC fabrication.