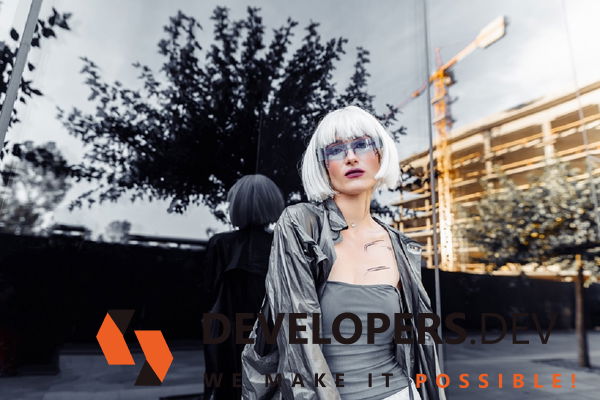
Designers using an integrated CAD + CAM solution can share their CAD models seamlessly with an in-house machinist or external manufacturer, and vice versa for manufacturers receiving and working across departments on receiving files via an integrated solution.
While ease of use is certainly the main benefit to consider when selecting such software solutions, there may also be many additional perks worth discovering. computer-aided design and computer-aided manufacturing
Computer-Aided Design (CAD)
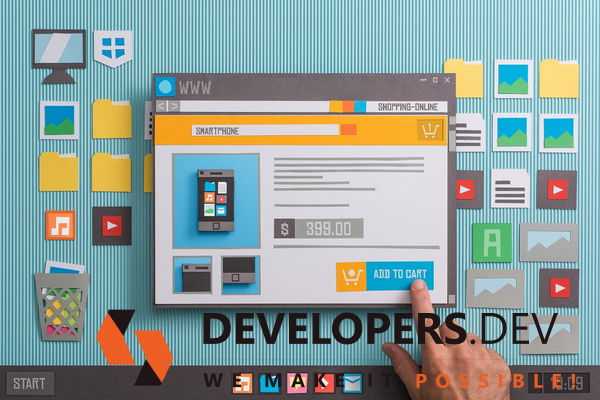
CAD system refers to computer software used for 3D product design.
Businesses using this technique can visualize potential designs using various materials before sharing images for collaboration or consultation worldwide. Once production decisions have been finalized, these designs are sent to Computer Aided Manufacture (CAM) machines so they may be produced.
Advantages of CAD:
- Saves Time: By employing computer-aided design software, time will be saved while better and more effective designs can be produced more rapidly than before.
- Easy Edits: As with any design project, changes may become necessary when editing drawings. Fortunately, computer-aided design software simplifies editing as errors are easily fixed and drawings modified easily.
- Reduced Error Percentage: Since CAD software uses some of the top tools, errors caused by manual designing are significantly decreased.
- Reduce Design Effort: Design effort has been significantly decreased thanks to software that automates most tasks associated with model creation.
- Code Reuse: Using computer tools for all aspects of this task makes code reuse much simpler; each part can be copied multiple times over and reused as many times as needed.
- Simple Sharing: With CAD system tools, saving and sharing files becomes much simpler - meaning theyll always be available when needed and without hassles or unnecessary complications.
- Increased Accuracy: Theres no questioning the fact that CAD software provides greater accuracy compared to manual drawings, giving designers tools for measuring the precision, skill, and accuracy of designs.
Disadvantages of CAD:
- Work may be lost when computers suddenly stop functioning as expected, leading to immediate work suspension.
- Work Environment Vulnerable to Hacking. / "Hack" Work may easily become vulnerable to viruses that compromise data systems and security breaches.
- Understanding and operating software takes time.
- Time and cost associated with training staff working on it can add up quickly.
- Software or Operating systems require regular updating for optimal functioning and optimal efficiency.
- Due to CAD/CAM systems, employees require less employment.
As other areas of technology emerge, we expect that computer-aided design (CAD) will also evolve over time, offering users more intuitive and straightforward experiences when using this equipment.
This may allow CAD equipment to serve more industries.
Want More Information About Our Services? Talk to Our Consultants!
Computer-Aided Manufacture (CAM)
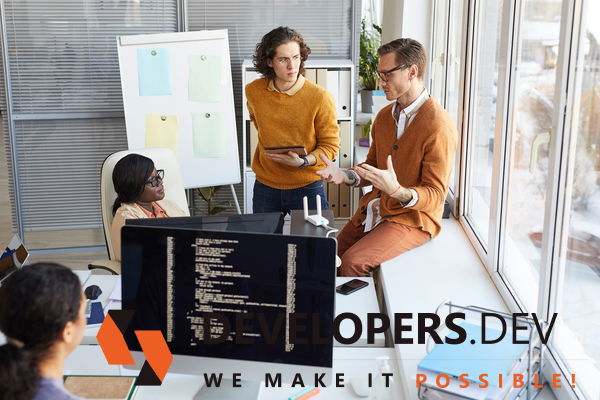
Computer Aided Manufacture CAM system involves using computers to control machines involved in producing goods.
Designs sent using this technique can then be processed by machines such as laser cutters, 3D printers, and milling machines for manufacturing purposes.
Computer Aided Manufacturing (CAM) plays a vital role in our physical world - products, parts, or places - from making airplane wings functionally feasible to giving cars their horsepower rumble.
When something needs making beyond just designing itself, CAM provides that solution. What happens behind the scenes will become clear as you read.
What Is Computer-Aided Manufacturing (CAM)? Computer Aided Manufacturing (CAM) is using software and computerized machinery to automate manufacturing processes.
As per this definition, it requires three components for any CAM system to function effectively. These are:
- Software that instructs a machine how to fabricate its products by creating toolpaths is known as production planning software.
- Industrial machinery that can convert raw material to finished product.
- Post Processing converts toolpaths into an executable language that the machine understands.
These components come together through human labor and skill. Still, weve spent decades perfecting manufacturing machinery that no other industry can match.
Advantages Of CAM
- Manufacturing requires minimal oversight and can even take place after hours.
- Manufacturing with less labor input reduces expenses on this front.
- Machines are highly accurate, making large batches of production repeatable repeatedly.
- Error rates are low, and machines may operate effectively for extended periods.
- Prototype models can quickly be created for detailed inspection before finalizing designs for manufacturing.
- Virtual machining enables us to evaluate machining routines and outcomes on screen virtually.
Disadvantages Of CAM
- It requires a substantial start-up expense and early investment.
- Machine maintenance is also expensive.
- High-level manual workers could become obsolete..
- Highly trained operatives and technicians are required to ensure proper tooling and setup procedures.
Differences Between CAD And CAM
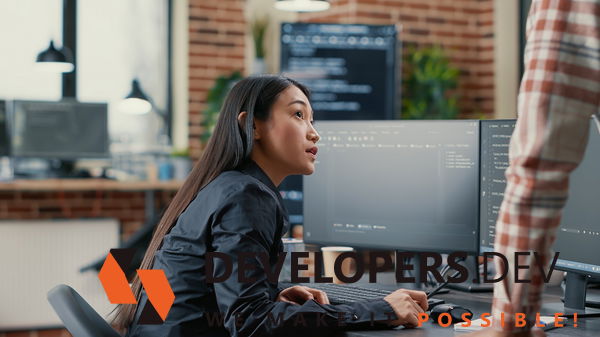
Computer-aided design (CAD) involves:
- Employing computers to transform an idea for a product into an engineering design that can be refined over time by manipulating.
- Analyzing.
- Refining geometric models created in this evolution process.
Meanwhile, Computer-Aided Manufacturing (CAM) utilizes computers to aid managers, manufacturing engineers, and production workers to automate production tasks while controlling machines and systems.
CAD system processes involve creating geometric models from scratch, translating their definitions, and defining, detailing, documenting, interface designing, and analyzing algorithms for use.
CAM utilizes geometric modeling programs (numeric control programs and interface algorithms), inspection processes, and process planning, assembly, and packaging services to complete its processes.
CAM systems involve controlling and managing physical processes, equipment, materials, and labor. In contrast, the CAD system entails product design conceptualization and analysis.
There is a wide array of CAD software, such as AutoCAD, Developers.dev Inventor, and CATIA. On the other hand, Siemens NX, Power MILL WorkNC, and SolidCAM are among the many examples of CAM programs.
CAD to CAM Process
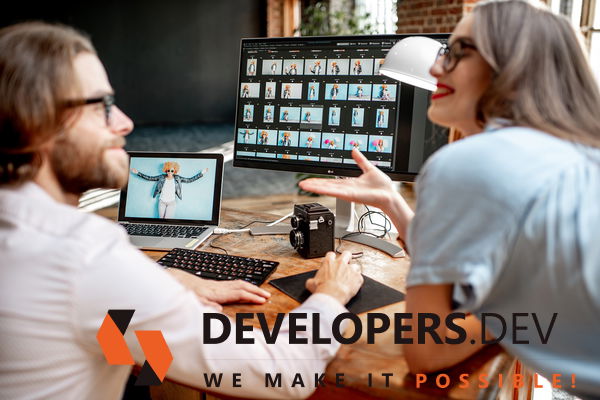
Without CAM, there would be no CAD. While CAD focuses on designing the look and function of products or parts, CAM addresses how these designs will be constructed; even the most elegant part created using your CAD tool could end up as nothing if production cannot occur efficiently enough with its respective CAM system.
At the heart of every engineering process lies Computer-Aided Design (CAD). Engineers create 2D or 3D drawings in this software program for projects as varied as crankshaft designs for an automobile engine or kitchen faucet inner structure detailing hidden electronics on circuit board designs.
Every CAD model contains physical properties, which CAM systems will later utilize for manufacturing purposes.
Once a design is finished in CAD, it can be loaded into the CNC cutting software (CAM). Traditionally, this involves exporting it and then importing it into CAM software; with Fusion 360, however, both functions exist within one environment, eliminating import/export requirements.
Once imported into CAM software, your CAD model is being readied for machining. CAD/CAM programming machining is the controlled transformation of raw material into specific forms by performing tasks like cutting, drilling, or boring to form shapes with precise geometry.
Computer Aided Manufacturing software creates models suitable for CNC milling by performing several actions, including:
Check if the model has any geometry errors impacting the manufacturing process.
- Toolpathing the model involves designing coordinates that the machine will follow during its machining process, known as a toolpath.
- Set machine parameters like cutting speed, voltage, and cut/pierce height.
- Nesting is when a computer-aided manufacturing (CAM) system decides on an optimal orientation for parts to maximize machining efficiency and save costs.
Once a model is prepared for machining, all necessary information is sent directly to a machine for production. However, we need to speak the machines language - G-code, in this instance, is its set of instructions that controls its action speed, feed rate, and coolants - before sending instructions in English directly.
Reasons To Switch To Integrated CAD/CAM
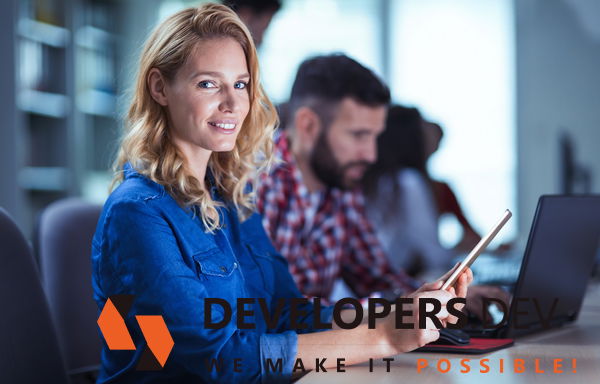
Over the past ten years, productivity in the manufacturing industry has decreased by 1.2% compared to 2.6% from seven previous years.
New emerging technology trends are upending engineering companies approach to product design, manufacture, and delivery; theres now more need than ever for innovation to help differentiate products in an ever more competitive environment. Increasing productivity remains essential, but finding efficient, cost-effective methods must always remain paramount.
Product design and manufacturing groups traditionally operated as separate functions, leading to frequent late-stage engineering changes and delays that severely impacted product costs, quality, and time to market.
Designers utilized CAD/CAM technology software while manufacturing departments utilized CAM applications for toolpath creation; once the design had been finished and handed off to manufacturing, data imports, translations, and conversions were often necessary due to standalone applications used by both departments; any required changes due to manufacturability issues would necessitate repeating this cycle for production to finish successfully.
An integrated CAD/CAM technology such as Developers.dev provides the ideal platform to bridge graphic design alterations and manufacturing teams and give users complete control of every design and manufacturing process step.
An integral CAD/CAM programming such as this is essential in providing users with fully associative CNC machining using solids-based models or neutral file formats like IGES or STEP; users can make complex design modifications easily while toolpaths will adapt themselves automatically.
Lets consider five major benefits integrated CAD/CAM systems can bring:
-
Integrated CAD/CAM Systems
Integral CAD/CAM systems save both cost and time by eliminating data translation steps between applications that operate on a 3D model, eliminating errors due to data translation in standalone systems, which often causes version issues with file versions not matching what CAM systems expect - thus leading to potential mistakes due to version discrepancies that cause version discrepancies that cause problems for each system.
Integrated CAD/CAM provides true associative machining (model associativity). This ensures any modifications made to a digital design are automatically updated in its respective CAM data, saving time-consuming rework due to design modifications.
-
Maintain Your Organization (avoid maintaining many disconnected files)
However, CAD/CAM technology files must remain up-to-date; keeping two separate program files up to date may prove challenging.
Updating both programs could prove time-consuming when designing changes occur, as each must be completely reprogrammed.
Integrated CAD/CAM systems help organize your data so you can easily collaborate in teams or parallel, responding more quickly to graphic design changes.
They feature repositories with file management to ensure everyone works on the latest industrial designers iteration; plus, using master models with associativity allows faster analysis, simulation, and cutter path updates without version conflicts.
-
Simplified Workflow
Standalone CAM systems tend to be process-oriented programming systems rather than feature-based. When selecting and creating operations such as rough milling a pocket, tools must first be selected before entering speeds, feed rates, and cutting parameters like depth into the system for roughing operations to begin.
Once rough milling operations have finished, other integrated tools may be selected and similar steps repeated until finishing operations are completed. Once all processes have been finished, the final code is generated for digital manufacturing operations.
As part of their programming practice when using standalone CAM systems, programmers often treat every part as a unique program despite it having characteristics similar to parts already programmed and machined.
Each programmer may have their take on how best to program this part, resulting in five distinct programmers, each creating five different inconsistent programs claiming theyre superior.
An integrated CAD/CAM system eliminates extra steps of data translation. It allows a smooth design-to-manufacture workflow using one interface for design and manufacturing processes.
This reduces training times and IT resources required to maintain multiple software packages and create more robust processes.
-
Automate The Manufacturing Processes
Standalone CAM systems tend to operate independently from industry-leading CAD solutions like SOLIDWORKS. They cannot take advantage of integrated CAD/CAM automation.
HCL Developers.dev integrated CAD/CAM technology automation allows manufacturers to take full advantage of automation; using tolerances, surface finish information, and product digital manufacturing information (PMI) on 3D models automatically creates CNC programs (including selecting tools with specific tool speeds/feeds to produce optimal toolpaths).
-
Integrated Validation Tools
Integrated CAD/CAM systems typically feature modules for validating designs before beginning CNC operations, with some integrated CAM systems offering G-code machine simulation directly within their CNC programming environments.
This helps eliminate dry runs for program validations, and setup times are dramatically cut down; once your G-code program has been verified via simulation directly into the CNC programming environment, it can run seamlessly without further validations needed before running it on the machine - saving scrap and improving overall quality! Integrated CAD/CAM is beneficial in terms of its five main benefits. It can facilitate better collaboration and knowledge transfer among design and manufacturing departments to produce designs that can be made correctly by considering late-stage manufacturability issues early in the design stages.
Doing this helps meet program schedules while simultaneously meeting quality goals while decreasing errors/rework issues/cost control objectives - when both disciplines use one system, which makes collaborating much simpler!
Benefits Of Integrated CAD/CAM
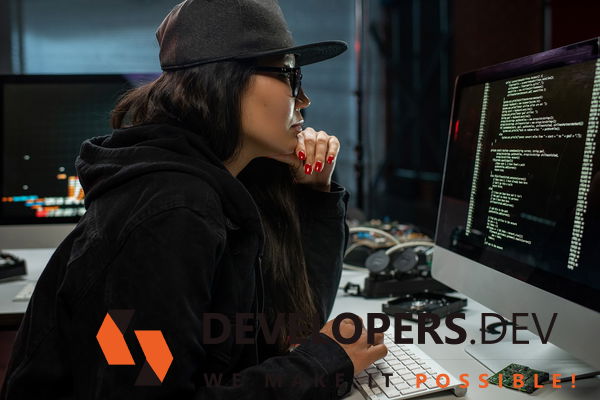
Integrating CAD/CAM software that encompasses electrode design and CMM programming into one seamless system can save time and effort in many situations.
Heres why:
- Eliminate extra and costly data translation steps between applications operating on the same 3-D model. Some systems offer complete suites of integrated applications for part design through mold design, NC programming, electrode design, and CMM inspection programming - helping reduce unnecessary workarounds.
- Automation can streamline more of the manufacturing authoring process: (a) automate NC and CMM programming directly on 3-D models by using design requirements such as GD&T and product manufacturing information (PMI), as well as color coding directly; and (b) store NC data within standard part 3-D model files so it can easily be updated according to its determined dimensions;
- Utilize integrated validation tools throughout the process. Integrated CAD/CAM systems offer tools to validate (and even improve) part and tool designs: manufacturability checks, injection molding simulation, and tool motion simulation with collision detection; before beginning production, NC data can be verified using integrated G-code driven machine tool simulation.
- Keep your data organized to allow teams and parallel work and faster response to design changes. Using a master model with associativity enables you to update mold design, NC programs, electrodes, and setup sheets whenever the CAD model changes; simple changes are updated instantly by associativity without needing reprogramming; multiple designers can be working simultaneously on one tool at the same time; plus NC programming may commence even before tool design has been finalized!
- Share knowledge among departments so designs are completed correctly the first time with manufacturing in mind, taking manufacturability into account. Having everyone work from the same system simplifies this task, yielding substantial advantages that could benefit everyone involved. Unfortunately, designers often underestimate the impact of their decisions on manufacturing processes.
Features Of Integrated CAD/CAM
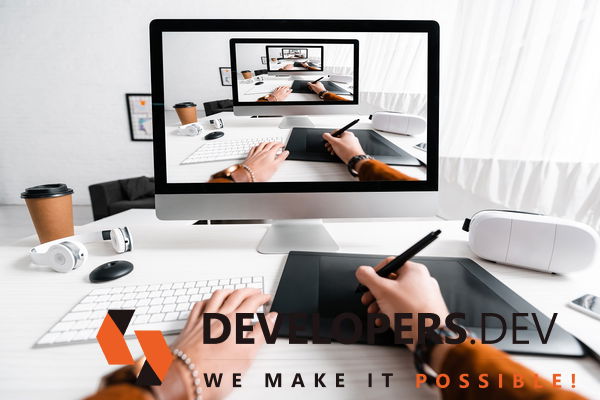
Features that are difficult to produce can increase job costs and require extra steps and NC programming time due to feature redesign.
NC programmers and designers who collaborate using the same system find it much simpler to collaborate, with some CAD/CAM systems featuring features for copying features into libraries for later use or creating customized features. NC programmers work alongside designers to specify features with manufacturability considerations in mind, saving design time by making features available as library items - knowing manufacturing will know exactly how they should be machined.
Starting fresh with one integrated CAD/CAM software and taking every step is where its true worth can shine through.
Users can achieve process benefits from doing everything with one system. Still, additional gains may include reduced training costs due to one consistent user interface thats easy to learn, simplified administration, and the convenience of dealing with just one vendor.
Eliminate Data Translation Issues
An integrated CAD + CAM technology eliminates the need to convert designs to neutral file formats like STEP or IGES or purchase costly data translators; working within one design system prevents losing information in translation processes or corrupting it during translation processes.
While you could invest in direct translators for other systems, their updates often lag those from CAD systems - potentially taking weeks or even months before your direct translator fully adapts to changes made to original file format changes in CAD format.
Model Associativity
An integrated CAD + CAM solution eliminates the need to convert files to neutral file formats like STEP or IGES or purchase costly data translators, meaning theres never an issue of losing or corrupting data during translation processes when working within one design system.
Although you could purchase direct translators for other systems, their updates could take weeks or months to catch up with changes to file format changes from CAD files.
Simplified Workflow
Removing extra steps of data translation and using the same interface as when designing creates an efficient design-to-manufacturing workflow, leading to less training, reduced IT maintenance resources, and an easier upgrade process.
Automate More Of The Manufacturing Process
Integrated CAD/CAM technology offers a more complete manufacturing workflow with automation.
Aside from creating cutter paths for CNC mills, integrated solutions may also output to other manufacturing processes like 3D printing, probing, and scanning.
Full Design Functions
Integration between CAD/CAM software provides many benefits to designers. Youll have access to full design capabilities, which you can utilize for modeling modifications, work holding/fixture creation, or adding extra runoff data before manufacturing begins.
Directly editing solid models can quickly alter filets and clearances on stamping dies for improved clearances, quickly alter mold portions to edit gating and cooling requirements, and quickly insert vises, clamps, tables, or any other manufacturing equipment with assembly functions quickly and efficiently.
Finally, drawing functions equipped with full dimensioning capability allow users to quickly produce 3D prints of their model for sharing among team members or others.
Integrated Validation Tool
Complete CAD/CAM systems may also feature modules to verify designs before initiating 2.5-axis, 3-axis, or 5-axis machining processes.
Structural analysis can determine whether or not an idea will fail before creation begins; plastic mold flow analysis validates mold designs before tooling is made for them.Simulations of CNC cutter paths help ensure collision-free runs by taking clamps, fixtures, and vises into account.
Stay Organized And Work In Teams
Full CAD/CAM systems feature file management and repository features that ensure everyone working on the latest design iteration works off a master model with associativity for faster analysis, simulations, cutter path updates, and without version conflicts.
Share Knowledge Between Departments
Design for manufacturability is integral to being efficient. Data sharing becomes simpler by having both design and manufacturing use the same system.
At the same time, collaboration ensures any potential manufacturing issues can be identified early during the design phase.
Cloud Functionality
Cloud-based CAD/CAM software such as Developers.dev offers many of the same advantages of an integrated CAD/CAM system.
As parts are shared and accessed from the cloud, version control of data is managed automatically; any time an update occurs while someone has it open, they will get a notification with updated details and will be informed accordingly. Products like Fusion 360 even come equipped with tools to perform stress or heat analyses!
Cloud-based CAD/CAM programming are ideal for collaborative efforts, providing access to anyone to view, measure, and comment on parts during design processes while assuring manufacturability.
Cloud systems update themselves automatically with lower IT maintenance costs than on-premise solutions, allowing editors or CNC programmers to edit/program models virtually anywhere - even from an airplane!
Technological Influence On Business Activity
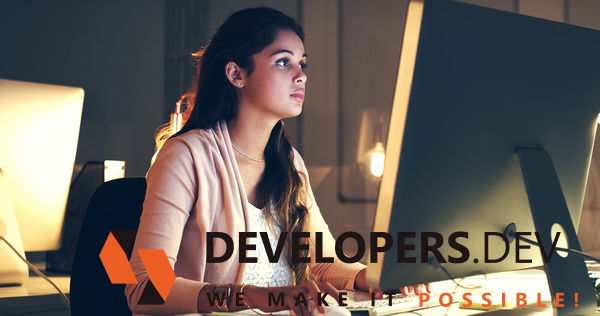
Technology advances at an ever-increasing pace. Businesses must keep abreast of new tech that might impact sales, costs, and marketing initiatives.
Technology disruption has enormously impacted businesses and business activity in general. Businesses of all types have taken note of adapting to these innovations to shape and influence their futures with them.
Technologies have made components such as manufacturing, communication, purchasing sales, and advertising simpler and more effective for them than before.
Technology advancements include:
- Email -Email allows people to communicate instantly by writing messages that can be delivered instantly as attachments to others; files can even be shared as attachments.
- Mobile Phones - mobile phones allow conversations to take place anywhere and at any time.
- Mobile Applications -Mobile applications (apps) for smartphones and tablets. Document creators, image capture, and banking transactions benefit from portable devices that simplify life. Businesses have taken steps to develop apps to engage in mobile commerce transactions.
- Websites - Websites (Web pages or "networks") allow businesses to communicate with customers and conduct commerce online by offering written and visual information in multiple forms on various media, providing businesses an avenue to interact directly with clients while opening up opportunities for e-commerce transactions.
- Social Media - Social Media (SM) platforms enable individuals and Websites (web pages or "networks") allow businesses to communicate with customers and conduct commerce online by offering written and visual information in multiple forms on various media, providing businesses an avenue to interact directly with clients while opening up opportunities for e-commerce transactions. Businesses can exchange ideas, information, and messages freely with one another online - creating an invaluable customer service resource.
- Web Conferencing - is an internet meeting that uses communications software to stream images and voices between participants at different places.
- Cloud Services - such as document editing and data storage software that operate remotely but can be accessed anywhere with internet connectivity allow for flexible use by anyone residing within any geographical boundary.
- Manufacturing - Modern technologies allow manufacturers to utilize various manufacturing techniques, from robots for car assembly to 3D printing to manufacture items like smartphones.
- Warehousing - As more businesses accept online orders, robotics have become an indispensable means of moving goods through warehouses and loading them onto vans quickly and safely.
- Electric Vehicles - Businesses have increasingly turned towards electric vehicles as an alternative fuel option, moving away from conventional petrol and diesel options.
Want More Information About Our Services? Talk to Our Consultants!
Conclusion
This review examined various CAD/CAM systems along with their advantages and drawbacks, with scanning, designing, and milling techniques being the most widely utilised options in addition to the CEREC system.
The benefits associated with each method were highlighted. The advantages of this technology outweigh its drawbacks, as these systems deliver improved comfort and aesthetics to patients.
CAD/CAM technology in dentistry has proven very promising. These systems have helped numerous dentists craft restorative and prosthetic devices that improve and sustain oral health, thus contributing to the overall enhancement and maintenance of oral well-being.Enhancing techniques and materials remains necessary to increase accuracy and durability in these machines, with further research required to assess the reliability, functionality, and usability of devices made using such machines.
Todays society demands high-quality prostheses and restorations made with CAD/CAM technologies at competitive pricing; therefore, further investigation must take place into these systems to provide patients with what they seek - quality dentistry at a more reasonable cost.
In light of this demand, further study of such systems must occur to provide patients with what they seek in dentistry services at an economical price.Making devices more cost-effective and improving material quality are among the goals of research-oriented CAD/CAM systems, offering consistent results and innovative techniques that benefit patient health in the long run.